Latest News
The process starts with a detailed needs analysis.
Individual die casting solutions emerge as part of a comprehensive and structured process that stretches from the analysis and development stages to production and finishing. In the product-related process, research and development as well as consulting and support are also implemented. Furthermore, the entire process is secured by continuous quality management. During the initial analysis, we look at the needs and expectations of our customers in detail.
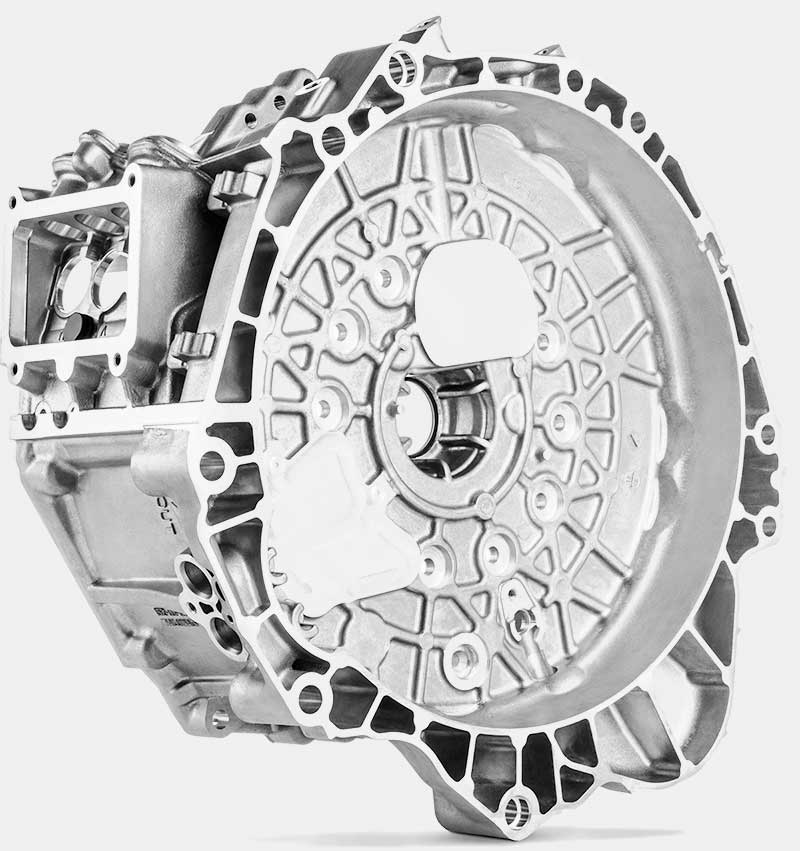
The development of materials is a high-tech process.
Within the comprehensive overall process, analysis is followed by the development stage. Here, a focus is placed on materials technology, engineering and laboratory activities that, for example, comprise state-of-the-art CT and spectral analyses as well as prototyping and sampling.
Materials technology
- Basic research of materials ↗
- Processing of secondary alloys (standard)
- Processing of primary alloys
Engineering and laboratory
- Material and component analyses
- Component development ↗
- Process development ↗
- FEM calculations
- Microscopy
- X-ray/CT analyses
- Spectral analyses
- Hardness testing
- Tensile testing
- Filling and solidificatin simulations
- Construction of die casting tools ↗
- Prototyping ↗
- Sampling ↗
Fully automated casting cells ensure stable production.
Within the value chain, development is followed by fully automated production. Here, we systematically pursue a zero-error strategy, which we guarantee for any requested quantity. This quality awareness is part of our corporate self-image that is also expressed in our quest to achieve continuous process and cost optimization.
- Furnace technology with its own decentralised melting concept
- Aluminium die casting (clamping force of 400 – 2‘200 tonnes)
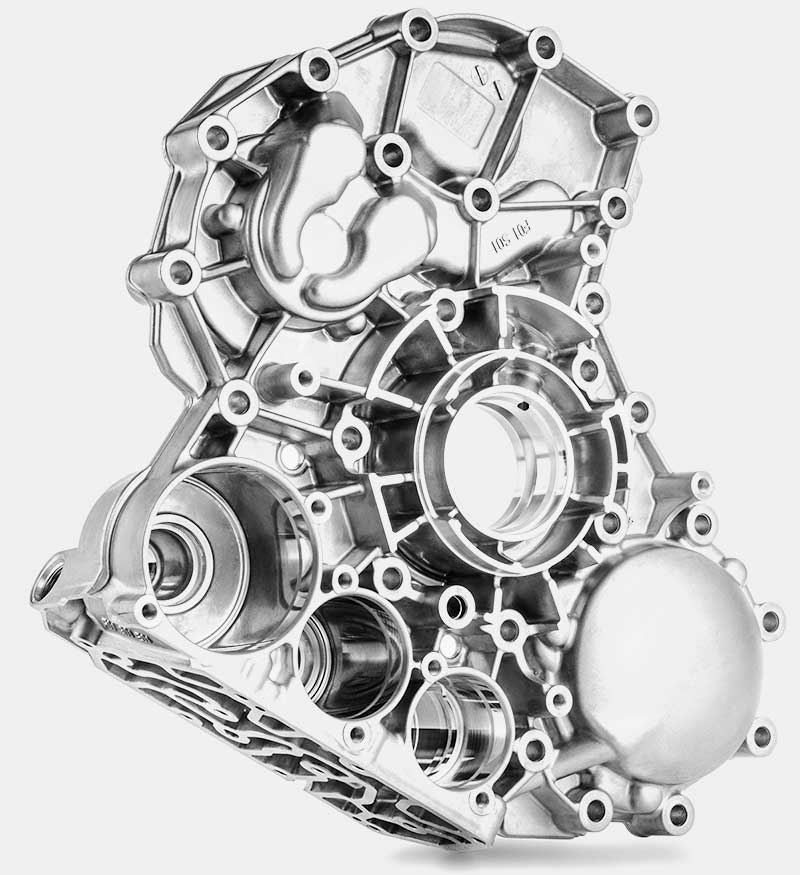
A perfect finish rounds off the error-free process chain.
Standard solutions generate standard results. This is not what we or our customers want. Within the framework of the overall process, we therefore offer diversified finishing work after production. This includes heat treatment and joining technology, mechanical processing and state-of-the-art surface technologies. We also ensure assembly up to the finished component or the desired module.
Heat treatment and joining technology
- Heat treatment (T4 to T6)
- Friction stir welding
- Adhesive bonding
Mechanical processing
- Deburring
- CNC milling
- CNC turning
- Washing processes without and with residual dirt requirements
- Leakage tests
Surface technology
- Functional coatings
- Decorative coatings
Assembly
- Assembly of modules